Now that I will be getting the final pieces for the custom sawari in next week and will be completing that part of the build, I figured I would start sharing some of the aspects of this unconventional sawari design! Of course like every other part of this build, I wanted even the sawari to have a unique design that has not been used yet in shamisen, and be one of the distinctive features of the Masamune shamisen build.
Originally going into the selection of the sawari, I knew that I would mess up installing the traditional azuma sawari, I just don’t think I could get those edges as straight and as clean as I would want. The en sawari makes installation easier, but I also like the aesthetics of the azuma sawari. Since I would also be using my own damascus screw cap, and due to the tenjin being thicker than average, I would need to design my own regardless. So, I figured why not combine elements from both the azuma sawari and en sawari and add a bit of a unique touch as well! Here is a CAD model of the final assembly:
Here is a cross-sectional view of the internal mechanism. The mechanism works the same as traditional, however there are some modifications to the inner cage and block pieces to make construction much simpler, as well as fit the geometry of the design. While the outside is circular like the en sawari, the inner block that raises and lowers is square.
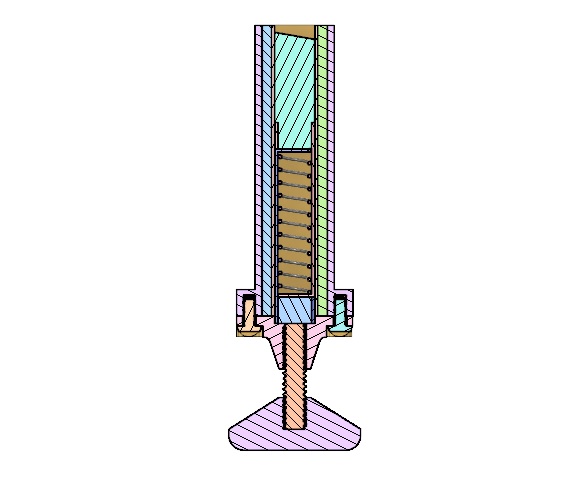
The traditional elevator mechanism has been modified for simpler construction. Both the inner cage and the elevator are identical, cut from square brass tubing which telescopically fits inside the square bore in the housing. The square brass tubing can be purchased from McMaster-Carr, and because the tubing is telescopic, each size fits into the next successive size perfectly, which guarantees a perfect fit between the elevator mechanism and the housing bore. Since the pieces are just cut from tubing, no soldering or brazing is required, making it much easier to build. Cutting the tubing, filing the edges flush, and bending the top flap down is all that is required.
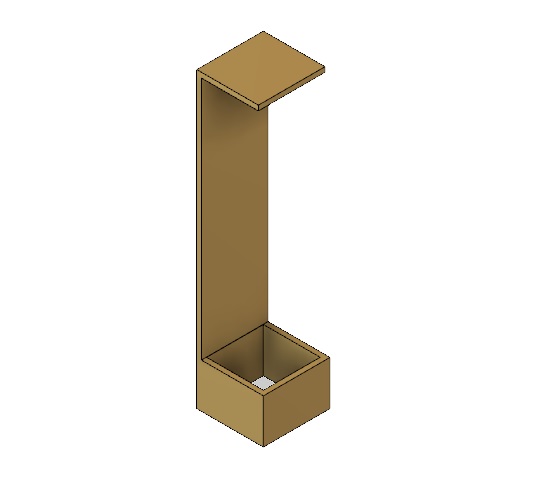
In addition, both the inner cage and elevator are identical and installed vertically mirrored to each other, with the inner cage soldered to the sawari base as traditional, and the elevator flipped upside-down, with a square block glued to the bottom, and a longer block glued at the top that interacts with the string. A single spring is placed inside between the bent tops of each piece.
A unique aspect of this design comes from the double-layered laminated housing, which consists of a 3/8" circular outer shell, and the square bore made from the prior mentioned square brass tubing. Each of the sides of the square inner tubing are laminated with thin pieces of ebony, and the whole assembly is turned down on a lathe and glued into the circular outer housing bore. This allows me to have simple installation like the en sawari, but prevents rotation of the inner piece when adjusted, while allowing me to achieve a similar aesthetic of the azuma sawari, using a square piece instead of a rectangle.
Coupled with the ebony square block in the center, when viewed from the top after installation, it creates the pattern shown below, alternating between the brass and ebony layers, creating an inset square inside the circular housing, giving the sawari a bit more interesting look.
And here is an idea of what it will look like after it is installed in the tenjin when viewed from the top:
The design could very easily be modified just using a square section to create a square sawari (which may be easier to carve out than a rectangle for the azuma sawari style), and due to the tubing used, makes construction of the mechanism overall simpler to build and fit perfectly inside the housing. More pictures of the real thing to come soon!